Ultraschall optimiert 3D-Druck
Projekt für stabile und langlebige Bauteile beim Laserauftragschweißen.
Ultraschall wird es in naher Zukunft ermöglichen, mit industriellen 3D-Druckern robustere, langlebigere und preiswertere Bauteile als bisher für Luft- und Raumfahrt, Werkzeugbau sowie weitere Branchen herzustellen. Um diese neue Technologie binnen drei Jahren zur Marktreife zu führen, haben sich Forschende aus Dresden, Hamburg und dem australischen Melbourne zu einem Forschungsverbund zusammengeschlossen. Ihr im Juni 2022 gestartetes Projekt UltraGrain zielt darauf ab, beim draht- und pulverbasierten Laserauftragschweißen eine maßgeschneiderte feinkörnige Mikrostruktur zu erzeugen, die eine Verbesserung der mechanischen Eigenschaften und der Korrosionsbeständigkeit einer Mehrzahl technischer Legierungen verspricht.
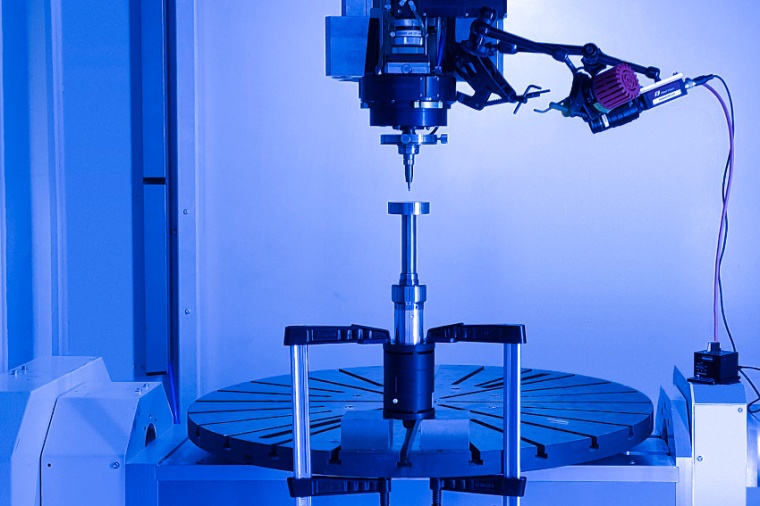
An dem mit vier Millionen Euro dotierten Projekt beteiligen sich das Fraunhofer-Institut für Werkstoff- und Strahltechnik IWS, die Fraunhofer-Einrichtung für Additive Produktionstechnologien IAPT und das RMIT Centre for Additive Manufacturing in Melbourne. „Uns ist dieses gemeinsame Projekt mit dem RMIT und dem Fraunhofer IAPT eine besondere Herzensangelegenheit“, betont Christoph Leyens, Institutsleiter des Fraunhofer IWS. Ähnlich sieht es Ingomar Kelbassa, Institutsleiter des Fraunhofer IAPT: „Sowohl das Fraunhofer IAPT als auch das Fraunhofer IWS arbeiten schon seit längerer Zeit über persönliche Kontakte mit den australischen Kolleginnen und Kollegen zusammen. UltraGrain ist jedoch nun das erste finanziell dotierte Vorhaben, das direkt in einen Transfer gemeinsamer Forschungsergebnisse in die industrielle Praxis münden soll.“
Angesichts der Zusammenarbeit mit einem exzellenten internationalen Institut, die sich hier anbahnt und vertieft, fördert die Fraunhofer-Gesellschaft das Projekt mit 1,5 Millionen Euro. Weitere 2,5 Millionen Euro steuern die australischen Partner zu. Die beteiligten Wissenschaftlerinnen und Wissenschaftler sehen großes Marktpotenzial in ihrem Kooperationsprojekt: „UltraGrain wird dabei helfen, Additive Manufacturing in eine breite industrielle Anwendung zu bringen“, prognostiziert Christoph Leyens. Die Projektmitarbeiter des RMIT Centre for Additive Manufacturing sind sehr optimistisch, was die Anwendung von Ultraschall auf die Mikrostrukturmanipulation angeht. Sie sind überzeugt, dass die nächste Generation der additiven Fertigung von Luft- und Raumfahrtteilen erheblich von der Einführung der Ultraschalltechnologie profitieren wird, die sie gemeinsam mit den Fraunhofer-Partnern entwickeln werden.
Dabei betreten die Forschenden technologisches Neuland. Um gezielt die innere Kornstruktur von 3D-gedruckten Bauteilen und damit deren mechanische Eigenschaften zu beeinflussen, kombinieren sie das bewährte draht- und pulverbasierte Laserauftragschweißen mit Ultraschall. Dafür senden sie während des additiven Auftragsprozesses zum Beispiel feine Vibrationen mit einer präzise definierten Frequenz durch das entstehende Bauteil. Der Ultraschall verhindert, dass sich darin säulenartige Strukturen bilden. Diese mikroskopisch kleinen Säulen im Material sind oft unerwünscht, da ihre einseitige Ausrichtung zu schlechteren mechanischen Leistungen führt. Unter Ultraschallwirkung hingegen bilden sich feinere, rund geformte Mikrokörner, die an den bearbeiteten Stellen nahezu gleichmäßig verteilt sind.
Diese equiaxiale Ausrichtung erhöht die mechanische und chemische Belastbarkeit der additiv erzeugten Werkstücke. Weil sich der Ultraschall gezielt steuern lässt, können die Bauteil-Designer zum Beispiel genau vorgeben, an welchen Stellen das Werkstück später im Einsatz großen Belastungen ausgesetzt sein wird. Dort können die Entwickler eine ultraschall-gesteuerte Kornstruktur einplanen, aber auch entscheiden, an welchen Stellen sie zu Gunsten einer schnelleren Produktion darauf verzichten können. Wichtig ist solch eine Gradierung, damit beispielsweise Gastanks von Raumsonden später einmal die besonderen Herausforderungen im Weltall über Jahre hinweg aushalten oder Werkzeuge in Autofabriken selbst hohen Punktbelastungen in der Massenproduktion widerstehen.
„Mit UltraGrain können wir Eigenschaften wie die Ermüdungsbeständigkeit, Festigkeit, Belastbarkeit und Duktilität verbessern und reduzieren die Rissanfälligkeit von additiv gefertigten Bauteile deutlich“, sagt Projektleiterin Elena López vom Fraunhofer IWS. Das Interesse aus der Wirtschaft an dem neuen UltraGrain-Verfahren ist bereits zum Projektstart groß. Der Industriebeirat setzt sich unter anderem aus international agierenden Unternehmen aus Luft- und Raumfahrt, Bahntechnik sowie weiteren Branchen zusammen. Erfahrungsgemäß gehören diese in den Beiräten von Fraunhofer-Projekten vertretenen Unternehmen oft zu den frühen Anwendern solcher neuen Technologien.
Fh.-IWS / JOL